Cashew Nut Cutting Machine: Complete Guide to Automation & Efficiency
The cashew processing industry has evolved significantly with the introduction of advanced cashew nut cutting machines. These specialized devices have revolutionized how raw cashew nuts are processed, offering unprecedented efficiency, reduced labor costs, and higher quality outputs. Whether you’re establishing a new cashew processing facility or upgrading existing equipment, this comprehensive guide covers everything you need to know about modern cashew cutting technology.
Understanding Cashew Nut Cutting Technology
Cashew nut cutting machines represent the critical first step in processing raw cashews, separating the valuable kernel from its tough outer shell. This mechanical process has replaced traditional manual cutting methods in most commercial operations, resulting in higher throughput and consistent quality.
Vietnamese Cutting Technology: The Gold Standard
The Vietnamese horizontal cutting technology has emerged as the industry benchmark for cashew processing. These machines utilize precision-engineered blades that move horizontally to slice through the cashew shell while preserving the integrity of the kernel inside. Vietnamese technology delivers superior results with broken rates below 3% and shell removal efficiency exceeding 95%.
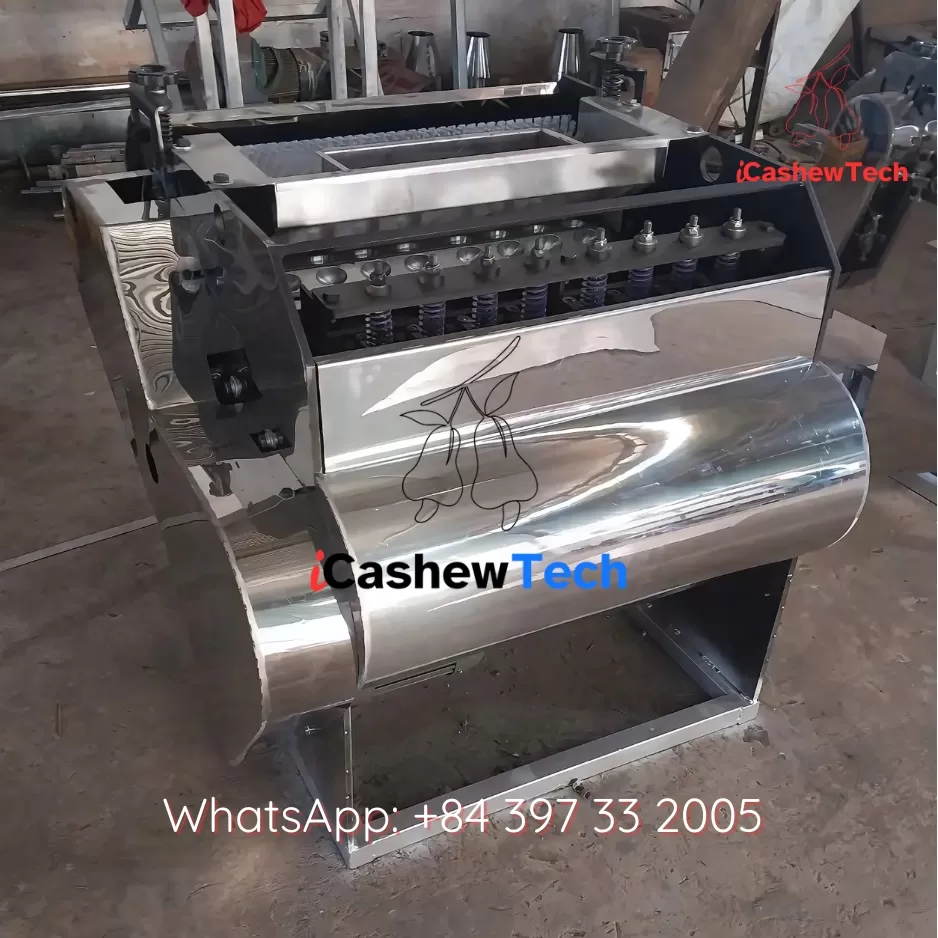
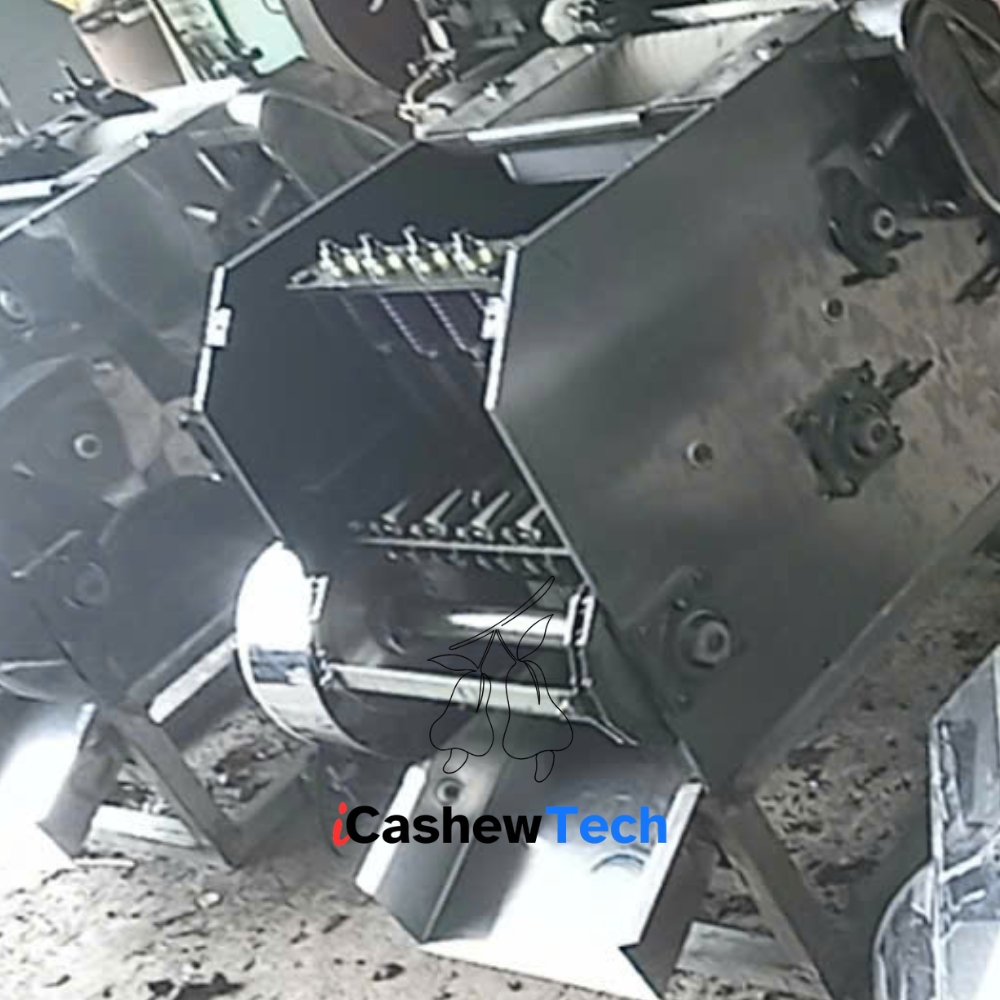
Key Components of Modern Cutting Machines
Modern cashew cutting machines feature several essential components designed for optimal performance:
- Cutting Blade System: Typically made from tungsten-based materials or special alloys that maintain sharpness and durability
- Feeding Mechanism: Automated systems that position cashews correctly for precise cutting
- Machine Body: Constructed from stainless steel or mild steel for durability and food safety compliance
- Transmission System: High-precision gears ensure consistent cutting action
- Power System: Energy-efficient motors that can operate on single-phase or three-phase power supplies
The integration of these components results in machines capable of processing between 20kg to 400kg of cashews per hour, depending on the model and configuration.
Types of Cashew Cutting Machines
The market offers various types of cashew cutting machines to suit different operational needs and budgets.
Automatic Cashew Cutting Machines
These high-capacity systems represent the most advanced technology available. They feature fully automated feeding, cutting, and separation processes with minimal human intervention.
Automatic machines typically offer:
- Production capacities of 80-400 kg per hour
- Integrated shell and kernel separation
- Computerized control systems
- Low broken rates (below 5%)
- Multi-blade configurations (4, 6, 10, or 12 blades)
Semi-Automatic Cutting Machines
These mid-range options balance automation with affordability, making them suitable for medium-scale operations.
Key features include:
- Capacities ranging from 40-80 kg per hour
- Partial automation of feeding or separation
- Moderate investment requirements
- Suitable for growing businesses transitioning from manual methods.
Manual Cashew Cutters
These entry-level machines require more operator involvement but come at a significantly lower price point, making them accessible for small-scale processors or startups.
Manual cutters typically offer:
- Capacities of 8-20 kg per hour
- Mechanical operation with minimal power requirements
- Lower initial investment
- Suitable for artisanal production or testing markets.
Technical Specifications and Performance Metrics
Understanding the technical aspects of cashew cutting machines helps in making informed purchasing decisions.
Production Capacity
Modern cutting machines offer varying throughput capabilities:
- Entry-level models: 80-120 kg/hour
- Mid-range models: 300-500 kg/hour
- High-capacity models: 400-700 kg/hour
Capacity requirements should be calculated based on your daily processing needs and operational hours.
Power Requirements
Power consumption varies by model:
- Single-phase options (220-240V): Ideal for smaller operations or areas with limited power infrastructure
- Three-phase options (380V): Better suited for industrial settings
- Power ratings typically range from 0.4kW to 0.75kW
Most modern machines are designed for energy efficiency, consuming as little as 0.4 units of electricity per hour of operation.
Cutting Efficiency Metrics
Performance is measured through several key metrics:
- Uncut ratio: Best machines achieve less than 10%
- Broken kernel ratio: Premium models maintain below 3-5%
- Shell removal rate: Top performers achieve 95-98% efficiency
These metrics directly impact profitability through higher yields of marketable cashew kernels.
Benefits of Automated Cashew Cutting Systems
Investing in modern cashew cutting technology offers numerous advantages over traditional processing methods.
Economic Advantages
The financial benefits extend beyond initial labor savings:
- Reduced labor costs through automation
- Higher throughput without quality compromises
- Improved yield of whole kernels increases market value
- Lower energy consumption compared to labor-intensive methods
- Extended equipment lifespan with proper maintenance
Quality Improvements
Modern cutting technology elevates the quality of processed cashews:
- Consistent cutting precision
- Lower contamination risk
- Reduced breakage preserves whole kernel value
- Minimal oil contamination during processing
- Uniform product quality across batches
Operational Efficiency
Streamlined processing offers significant operational benefits:
- Continuous operation capabilities
- Reduced processing time from raw nut to finished kernel
- Easy integration with other processing steps
- Minimal operator training requirements
- Lower maintenance needs with robust construction
Choosing the Right Cashew Cutting Machine
Selecting the appropriate machine requires careful consideration of several factors to ensure optimal performance and return on investment.
Assessing Your Processing Needs
Before purchasing, evaluate:
- Daily/monthly processing volume requirements
- Available factory space
- Existing infrastructure (power supply, complementary equipment)
- Labor availability and skill level
- Budget constraints
- Long-term business growth projections
Key Features to Consider
Important features that differentiate cutting machines include:
- Blade material and durability (specialty alloys offer longer life)
- Construction quality (stainless steel vs. mild steel)
- Automation level of feeding and separation systems
- Ease of maintenance and availability of spare parts
- Adaptability to different cashew sizes and qualities
- Warranty terms and technical support availability
Understanding Total Cost of Ownership
Look beyond the initial purchase price to evaluate:
- Spare part requirements and costs (especially cutting blades)
- Power consumption over time
- Maintenance requirements
- Labor needs for operation
- Expected equipment lifespan
Integration with Complete Cashew Processing Lines
For maximum efficiency, cashew cutting machines can be integrated into comprehensive processing systems.
Components of a Complete Processing Line
A fully automated cashew processing facility typically includes:
- Raw cashew reception and cleaning
- Cooking/steaming systems (pressure or non-pressure)
- Cutting machines
- Shell and kernel separation systems
- Peeling equipment
- Grading and sorting machinery
- Packaging solutions
Automation Considerations
The degree of automation across the processing line affects:
- Overall throughput consistency
- Labor requirements
- Quality control capabilities
- Investment levels
- Scalability options
Maintenance and Operational Best Practices
Proper maintenance ensures optimal performance and longevity of cashew cutting equipment.
Routine Maintenance Schedule
Implement a regular maintenance program including:
- Daily cleaning and inspection
- Weekly lubrication of moving parts
- Bi-weekly blade inspection
- Blade replacement or resharpening every 15 days
- Complete system overhaul every 3-6 months
Operator Training Requirements
Proper training should cover:
- Safe operation procedures
- Basic troubleshooting
- Optimal feeding techniques
- Quality control monitoring
- Basic maintenance tasks
- Emergency shutdown procedures
Global Market and Suppliers
The cashew cutting machine market features manufacturers from several key regions, each with distinct advantages.
Leading Manufacturing Regions
Major suppliers come from:
- Vietnam: Known for cutting-edge technology and high efficiency
- India: Offers a range of options from manual to fully automated
- China: Provides competitive pricing with varying quality levels
Major Suppliers and Their Specializations
Notable manufacturers include:
- Mekong Technology Vietnam: Specializes in high-capacity automatic systems
- Rami International (India): Offers Vietnamese-style machines with local support
- Cashew Tech: Provides complete processing lines with integration services
- Locus Exim: Manufactures both entry-level and advanced models
FAQs About Cashew Nut Cutting Machines
What is the average return on investment for an automatic cashew cutting machine?
Most processors report ROI within 1-2 years for automatic machines, depending on production volume and local labor costs. The higher initial investment is offset by increased productivity, reduced labor expenses, and improved kernel quality that commands better market prices.
How do Vietnamese cashew cutting machines differ from other technologies?
Vietnamese cashew cutting technology utilizes a horizontal cutting approach with precision-engineered blades that achieve significantly lower breakage rates (below 3%) compared to other methods. These machines typically feature superior construction quality, with components made from special alloys and stainless steel for durability and food safety.
What maintenance do cashew cutting blades require?
Cutting blades typically need resharpening every 15 days of operation. Quality blades can be reused for approximately 3 months with proper maintenance before requiring replacement. Regular cleaning and proper alignment are essential for optimal performance and longevity.
Can cashew cutting machines handle different cashew sizes?
Yes, most modern machines can be adjusted to accommodate different cashew nut sizes. Higher-end models feature adjustable guide bars and mold blades that can be calibrated for specific cashew dimensions, typically categorized as sizes A, B, C, and D.
What is the power consumption of a typical cashew cutting machine?
Most modern cashew cutting machines are energy-efficient, consuming approximately 0.4 to 0.75 kW per hour of operation. Single-phase machines typically operate at 220-240V, while industrial models may require three-phase power at 380V.
How many workers are needed to operate a cashew cutting line?
The labor requirement varies based on automation level:
- Manual machines: 1-2 operators per machine
- Semi-automatic systems: 1 operator can manage 2-3 machines
- Fully automatic lines: 1-2 operators can oversee the entire cutting and separation process
Cashew nut cutting machines represent a critical investment for processors seeking to improve efficiency, quality, and profitability. The technology continues to evolve, with Vietnamese horizontal cutting systems setting new standards for performance and reliability.
When selecting a machine, consider not only the initial purchase price but also long-term factors such as processing capacity, energy efficiency, maintenance requirements, and integration capabilities. Proper operator training and routine maintenance are essential to maximize equipment lifespan and maintain optimal performance.
For processors of all sizes—from small-scale operations to industrial facilities—there are suitable cutting machine options available that can transform raw cashew processing from a labor-intensive task to an efficient, high-yield operation with significant return on investment potential.